Management philosophy
NIPPON KYOHAN KOGYO aims to bring happiness to all people and achieve sustainable development.
- "All" means employees, their families, our business partners, and local communities.
- "Fulfillment" means finding joy and delight in working for and with this company.
- "Continued growth" means maintaining strong and stable management.
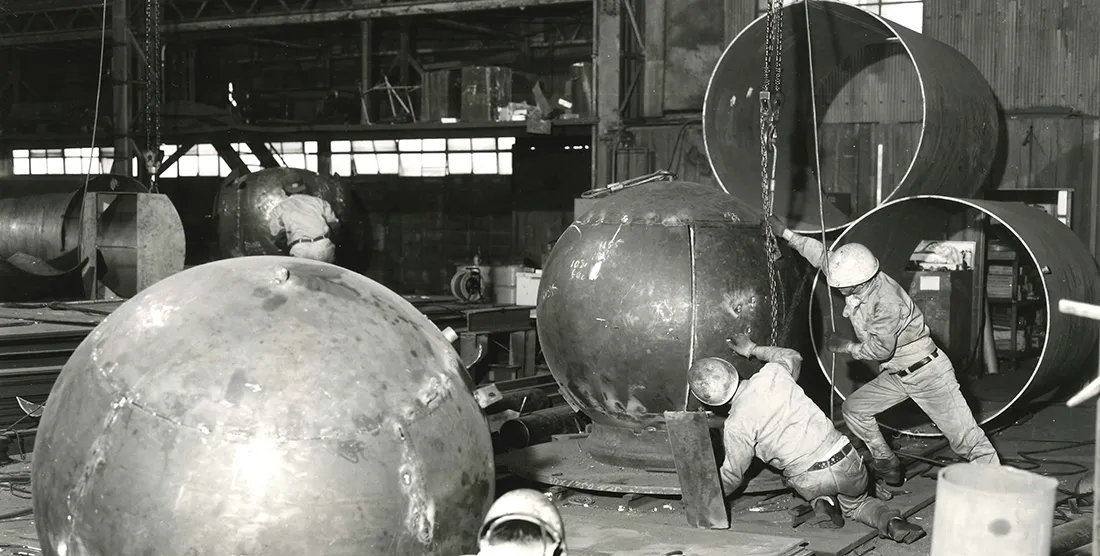
Employee charter
We pledge to do the following
- Seek to surpass customer expectations at all times.
- Maintain the trust of our customers.
- Continue to seek out and tackle new challenges.
- Create an atmosphere that allows forthright communication.
- Foster comfortable and fulfilling working environments.
- Seek to build a company in which everyone can take pride.
- Act in accordance with basic principles.
- Ensure thoroughgoing compliance with laws and regulations and build strong ties to local communities.
- Seek to ensure safety and health.
Quality policy
To achieve quality, cost, delivery times, and safety that satisfy customers, we seek to clearly set forth our organization and divisions of roles and responsibilities and to make sure that all employees enhance their skills and strive side by side to continuously improve the quality management system.
- We are striving every day to strengthen quality control; for example, we were the first in the head plate industry to acquire ISO 9001 certification.
- In addition to the ISO certification, we also have registered JIS mark certification as well as Class I pressure vessel manufacture certification.
- Our processing of special materials, such as titanium, copper, aluminum, nickel, Inconel, Incoloy, and zirconium, is supported by long years of experience and past proven performance, and is highly rated by customers with satisfaction.
Certification bodies | Certification types and levels |
Japan Quality Assurance Organization |
JIS B 8247 Formed head for pressure vessel (JIS mark certification) Certificate No.JQ0508121 |
---|---|
Labor Standards Bureau of the Ministry of Health, Labor and Welfare |
First class pressure vessel manufacturing license Head plates for boilers and first class pressure vessels |
High Pressure Gas Safety Institute of Japan ISO Registration Center |
ISO 9001:2008 / JIS Q 9001:2008 Registration No.95QR・014 Production of moldings for vessels by pressing or spinning Design and production of pressure vessels and welded structures |
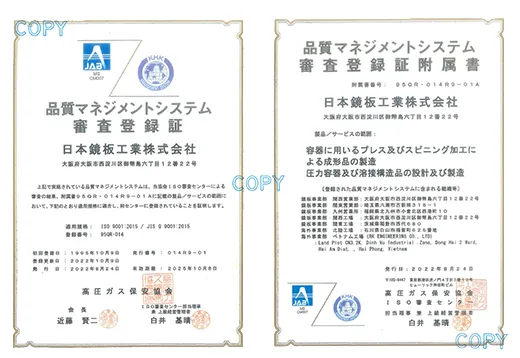
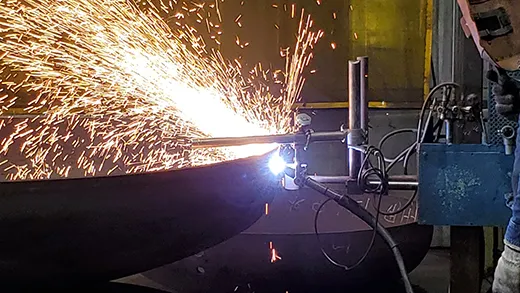
President’s
message
For more than a half century, Nippon Kyohan Kogyo has produced and sold the lids used on both ends of tanks for pressure vessels.
We have constantly focused on the cold working process through these years, a process that imposes minimal strain on materials. That’s because our first priority is the performance and safety of the tanks, key equipment found at production facilities.
While staying true to our fundamental philosophy, we’ve continued to restructure our factories and upgrade production equipment to enhance productivity and reduce costs. Making the most of our head plate production technologies, we’ve also begun producing various pressure vessel tanks and products for the food and pharmaceutical industries.
In 2012, we set up a factory in Vietnam to produce pressure vessels and other products. We’re dedicated to keeping up to date with changing needs while remaining true to our fundamental philosophy. Our pledge to our customers is to continue working to refine our technologies and organization and to provide products essential to their work.
We look forward to your steadfast support and encouragement.
President
Saburo Kobayashi
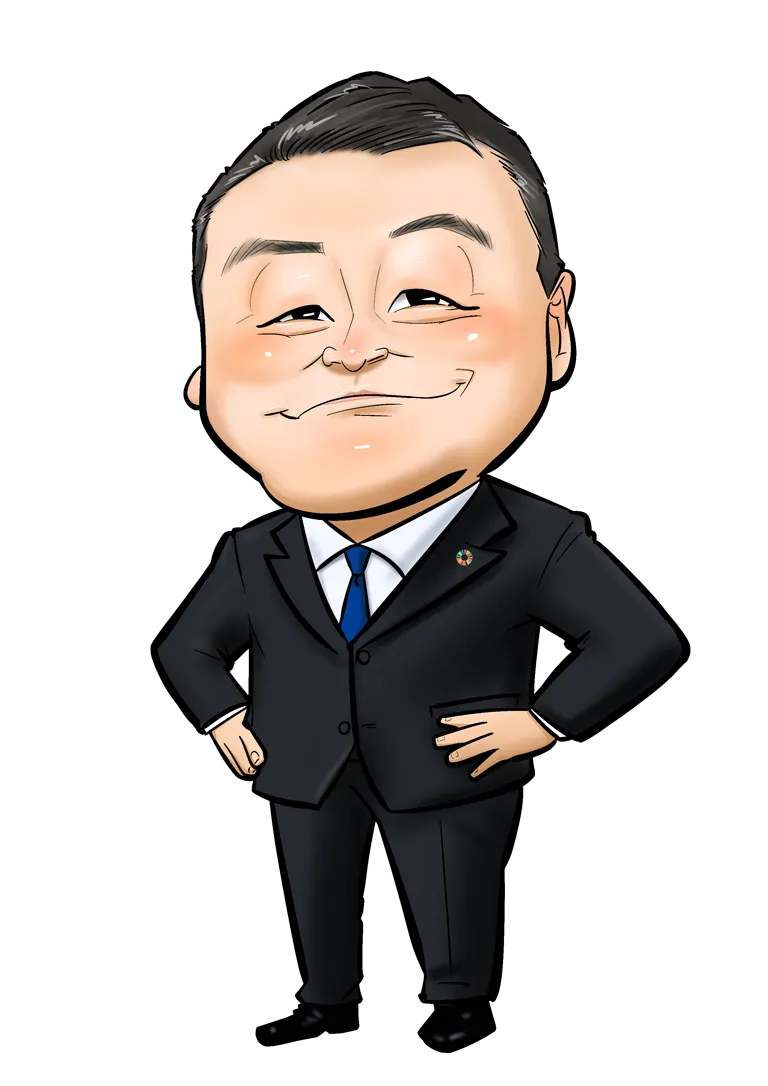
SDGs declaration of Nippon Kyohan Kogyo Co., Ltd.
We support the Sustainable Development Goals (SDGs) advocated by the United Nations, and declare that we will continue to work to solve various issues in pursuit of realizing a society in which people and nature can harmonize and develop under the management philosophy of “Nippon Kyohan Kogyo strives to achieve continuing growth and to bring fulfillment to all.”
About SDGs and CSR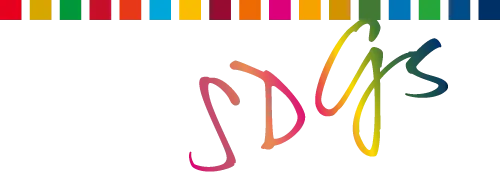
Corporate profile
Company name | NIPPON KYOHAN KOGYO CO.,LTD |
---|---|
Address | Head office:12-22 Mitejima 6-chome, Nishi-yodogawa-ku, Osaka-shi, Osaka |
Capital | Approx. 90 million yen |
Annual turnover | 4 billion yen |
Date of establishment | February 1, 1965 |
President | Saburo Kobayashi |
Number of employees | 125 |
Banks | Nanba branch, Mitsui Sumitomo Bank |
Business | ISO 9001: 2008/JIS Q 9001: 2008 No. 95QR-014“Production of moldings for vessels by pressing or spinningDesign and production of pressure vessels and welded structures”JIS mark certification: JIS B 8247Certificate No. JQ0508121Boiler and first class pressure vessel manufacturing licenseWelding certificate under the Electricity Business ActWelding certificate under the Designated Equipment Inspection Rules of the High Pressure Gas Safety Act |
[Technical partner] Company name |
Taiwan End-Plate Co., Ltd. |
Address | Taipei Factory:No. 32, Lane 102, Sec. 2, Kuang Fu Road, San Chung Dist., New Taipei City, Taiwan, R.O.C. |
Date of establishment | August 1, 1967 |
Capital | NT$60 million |
Certificates |
|
Offices and factories
-
Head office
NIPPON KYOHAN KOGYO CO.,LTDHead office - General Affairs
Overseas Sales dept.12-22 Mitejima 6-chome, Nishiyodogawa-ku, Osaka City, Osaka 555-0012, Japan
Tel: 81-6-6472-4772 (main)
Fax: 81-6-6477-1430Head Plate Sales dept./Kansai Sales Office 12-22 Mitejima 6-chome, Nishiyodogawa-ku, Osaka City, Osaka 555-0012, Japan
TEL: 81-6-6471-6031 (main)
FAX: 81-6-6472-1996 -
Kanto Sales Office
Head Plate Sales dept./Kanto Sales Office
Overseas Sales dept.2F, Tanizuka Collina, 1-9-1 Sezaki, Soka-shi, Saitama 340-0022, Japan
TEL: 81-48-949-6305(main)
FAX: 81-48-949-6516 -
Kyushu Sales Office
Head Plate Sales dept./Kyushu Sales Office 10 Nishiminato-cho, Kokurakita-ku, Kitakyushu-shi 803-0801 ,Japan
TEL: 81-93-561-1480(main)
FAX: 81-93-561-4476 -
Manufacturing dept./Kansai Factory
Manufacturing dept./Kansai Factory 6-12-22 Mishijima, Nishiyodogawa-ku, Osaka-shi, Osaka 555-0012 ,Japan
TEL: 81-6-6471-7454(main)
FAX: 81-6-6472-1980 -
Manufacturing dept./Kanto Factory
Manufacturing dept./Kanto Factory 680 Nishidai, Inashiki-shi, Ibaraki 300-0726, Japan
TEL: 81-299-78-3501(main)
FAX: 81-299-78-3554 -
Manufacturing dept./Hokuriku Factory
Manufacturing dept./Hokuriku Factory
Overseas Sales dept.625 Fukudome-cho, Hakusan-shi, Ishikawa 924-0051, Japan
TEL: 81-76-277-1200(main)
FAX: 81-76-277-1831
Customers
- NGK CHEMITECH, LTD.
- N.Y.K Co., Ltd.
- Kajiwara Kogyo Co., Ltd.
- Kawasaki Heavy Industries, Ltd.
- Sewon Giyeon Co.,Ltd.
- Kanematsu Engineering Co., Ltd.
- Kimura Chemical Plants Co., Ltd.
- Kyokuto Kaihatsu Kogyo Co., Ltd.
- Kido Co., Ltd.
- Cryo One Inc.
- Kurita Water Industries Ltd.
- Kotobuki Techrex, Ltd.
- Komatsugawa Chemical Engineering Co., Ltd.
- Sasakura Engineering Co., Ltd.
- Samson Co., Ltd.
- Sanwa Industries Corporation, Ltd.
- Sankyu Inc.
- Shimakura Iron Works Co., Ltd.
- KOBELCO Eco-Solutions Co., Ltd.
- ShinMaywa Industries, Ltd.
- Shinryo Corporation
- Japan Marine United Corporation
- Sumitomo Seika Chemicals Co., Ltd.
- Taiyo Nippon Sanso Corporation
- Takasago Chemical Engineering Co., Ltd.
- Tanabe Engineering Corporation
- Tamada Industries, Inc.
- Daido Steel Co., Ltd.
- Tanico Corporation
- Chugoku Kogyo Co., Ltd.
- Tsurumi Manufacturing Co., Ltd.
- Teijin Engineering Ltd.
- Topy Enterprises, Ltd.
- Toho Car Corporation
- Japan Chemical Engineering & Machinery Co., Ltd.
- Nippon Dry-Chemical Co., Ltd.
- Hirakawa Corporation
- Fuji Kohki Co., Ltd.
- Futaba Manufacturing Co., Ltd.
- Hosokawa Micron Corporation
- Hokko Kakouki Co., Ltd.
- Mitsui E&S Machinery Co., Ltd.
- Mitsubishi Heavy Industries, Ltd.
- Mitsubishi Materials Techno Corporation
- Miyake Industries Co., Ltd.
- Motomura Manufacture Co.,Ltd
- YASUDA FINE’TE Co., Ltd.
- Rozai Kogyo Kaisha, Ltd.
History
1959 | Nihon Tekko Co., Ltd., our predecessor, established at the address of the present headquarters |
---|---|
1961 | Cold spinning production line set up; head plate operations begin. |
1962 | Second cold spinning production line added Nihon Tekko Kyushu Factory opens in Kokura, Kitakyushu-shi. |
1963 | Cold spinning production line added at Headquarters Factory |
1964 | Cold spinning production line added at Kyushu Factory Cold spinning production line added at Headquarters Factory |
1965 to 1966 | Head Plate Department spun off as Nippon Kyohan Kogyo Co., Ltd.; Nippon Kyohan Kogyo begins operating. Kyushu Branch opened in Kokura |
1967 | Established Taiwan End-Plate Co., Ltd., a joint venture, in Taipei, Taiwan Opened Hokuriku Branch in Kanazawa-shi, Ishikawa |
1968 | Taipei Factory at Taiwan End-Plate completed and cold spinning production line installed Hokuriku Factory completed in Matto-shi (present Hakusan-shi), Ishikawa; cold spinning production line installed. Factory begins operating as part of the Hokuriku Division. |
1969 | Large West German flanging machine installed at Headquarters Factory Taipei Factory at Taiwan End-Plate installs second cold spinning production line. Construction of a factory with two production lines, including a West German large flanging machine, begins in Yashio-shi, Saitama. |
1970 | Kanto Factory (former Kanto Factory 1) completed; Kanto Division established. Production and sales of head plates begin. |
1972 | Taipei Factory at Taiwan End-Plate installs production equipment for large spherical tanks. Kanto Factory (former Kanto Factory 1) achieves JIS mark certification. |
1973 | Nihon Tekko relocated; the headquarters assumes oversight of head plate factory. Headquarters Factory introduces fully automatic dishing press with manipulator made in West Germany. |
1974 | Headquarters Factory introduces West German mid-sized flanging machine. |
1975 | Kanto Factory (former Kanto Factory 1) introduces manipulator for fully automatic dishing press. |
1976 | Hokuriku Factory obtains first class pressure vessel manufacturing license from the Labor Ministry (the present Health, Labor and Welfare Ministry). |
1977 | Headquarters Factory spun off from the headquarters to Kansai Division and Kansai Factory; Kyushu Branch incorporated into Kansai Division. Kanto Factory (former Kanto Factory 1) obtains first class pressure vessel manufacturing license from the Labor Ministry (the present Health, Labor and Welfare Ministry). Construction of a factory with large spherical tank production equipment and hot/cold spinning head plate production equipment begins in Kaosiung, Taiwan. |
1978 | Kaosiung Factory completed in Taiwan. Operations begin. |
1979 | Construction of Kanto Factory 2 begins in Ibaraki Prefecture. |
1980 | Completion of Kanto Factory 2. The factory launches planned production as a cold one press forming factory using 3,000-ton fully automatic double-action deep drawing hydraulic press. |
1981 | Kanto Factory 2 achieves JIS mark certification. |
1982 | Large fully automatic dishing press with manipulator installed at Kansai Factory |
1985 | Large fully automatic dishing press with manipulator installed at Kanto Factory 1 |
1986 | Completion of canning factory at Hokuriku Factory (Stage 1) |
1987 | Kansai Factory installs 800-ton fully automatic die cushion deep drawing hydraulic press. Factory begins planned production with small-diameter cold one press forming. Canning factory completed at Hokuriku Factory (Stage 2) |
1988 | Kyushu Factory introduces manipulator for fully automatic press. |
1990 | Kanto Factory 1 introduces mid-sized flanging machine. Canning factory completed at Hokuriku Factory (Stage 3) Hokuriku Factory introduces self-traveling dual welding robot and laser cutting machine. |
1991 | Kanto Factory 1 obtains boiler welding and manufacturing license from the Labor Ministry (the present Health, Labor and Welfare Ministry). |
1993 | Kanto Factory 2 for 9,000-ton hydraulic press completed |
1994 | Kanto Factory 2 begins operating 9,000-ton fully automatic double-action deep drawing hydraulic press; also begins planned production of products of diameters of 2,000+ mm. |
1995 | Kansai Division obtains ISO 9002 certification, a first for the head plate industry. |
1997 | Kanto Factory 2 upgrades 3,500-ton fully automatic double-action deep drawing hydraulic press. |
1999 | Kansai Factory introduces special spinning machine. |
2000 | Materials cutting factory completed at Kanto Factory 2 Kanto Factory 2 introduces NC plasma cutting equipment. |
2001 | Kanto Factory 2 introduces laser cutting machine. |
2002 | Kanto Factory 2 introduces 1,800-ton fully automatic deep drawing hydraulic press with die cushion. Kanto Factory 1 introduces mid-sized special spinning machine. |
2005 | Sales Department for Head Plate Division registered for ISO 9001 assessment |
2006 | Spinning yard factory completed at Kanto Factory 2 Kanto Factory 1 relocated to and merged with Kanto Factory 2; collective operations renamed Kanto Factory |
2007 | Offices at Kanto Factory and Kanto Sales Department renovated Kanto Factory at Head Plate Division registered for ISO 9001 assessment Head Plate Division obtains ISO 9001 certification for all departments. Kanto Factory upgrades 300-ton fully automatic deep drawing hydraulic press. |
2008 | Hokuriku Factory upgrades 1,000-ton hydraulic press. |
2009 | Chemical Engineering Division obtains ISO 9001 certification. |
2011 | Representative office opens in Hanoi, Vietnam. |
2011 | RK Engineering Co., Ltd., a Vietnam-based affiliate, established in Hai Phong, Vietnam Kanto Factory introduces mid-sized turning lathe. |
2012 | Kansai Factory upgrades 1,000-ton large fully automatic dishing press with manipulator. |
2013 | RK Engineering Co., Ltd. introduces 300-ton fully automatic dishing press with manipulator, a mid-sized spinning machine, and a heat treatment furnace. Kansai Factory introduces bending machine. |
2014 | RK Engineering Co., Ltd. introduces submerged arc welding machine with manipulator. |
2015 | Hokuriku Factory introduces a 200-ton press brake. Kansai Factory introduces plasma welding machine. |
2017 | The Kanto Factory introduces a German-made, large-size flanging machine. |
2019 | The Kansai Factory introduces an Italian-made 300-ton press. The Vietnam-based affiliate RK ENGINEERING CO., LTD. introduces a vertical precision milling machine. |
2022 | The Kanto Factory introduces an Italian-made 400-ton press. |